オキシムエステル型 光重合開始剤
「Nikkacure」開発ストーリー
当社が独自に研究開発したオキシムエステル型光重合開始剤「Nikkacure」
ラジカル型光重合開始剤の中で、特に高感度とされるオキシムエステル型の開発に成功しました。h線(405nm)に大きな吸収を持ち、フォトレジストをはじめ、幅広い用途で使用されています。ゼロから新製品立ち上げまでの製品開発の道のりをご紹介します。
PROJECT
MEMBER
登場メンバー
-
営業部 木村 -
開発室 田口 -
製造部 有本 -
製造部 木下 -
製造部 溝北 -
製造本部 中本
「Nikkacure」の開発に至ったきっかけを教えてください。
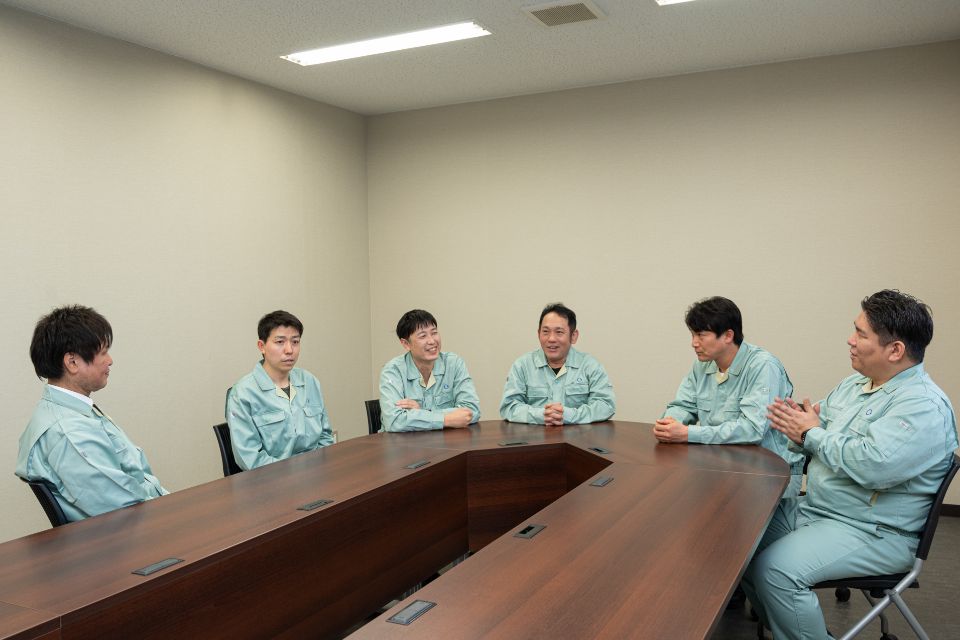
製品開発に皆さんはどのように関わっていましたか?
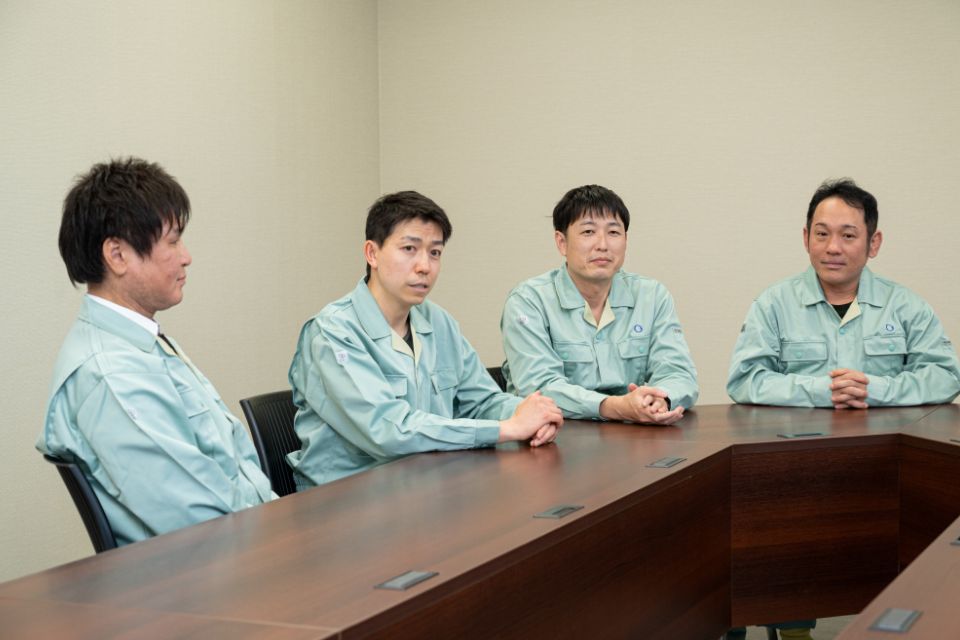
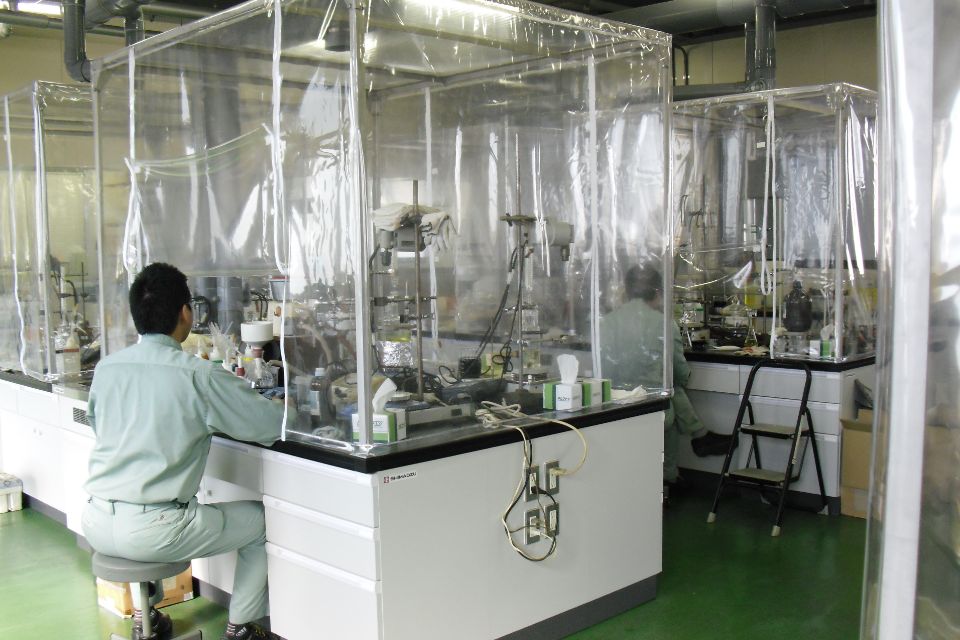
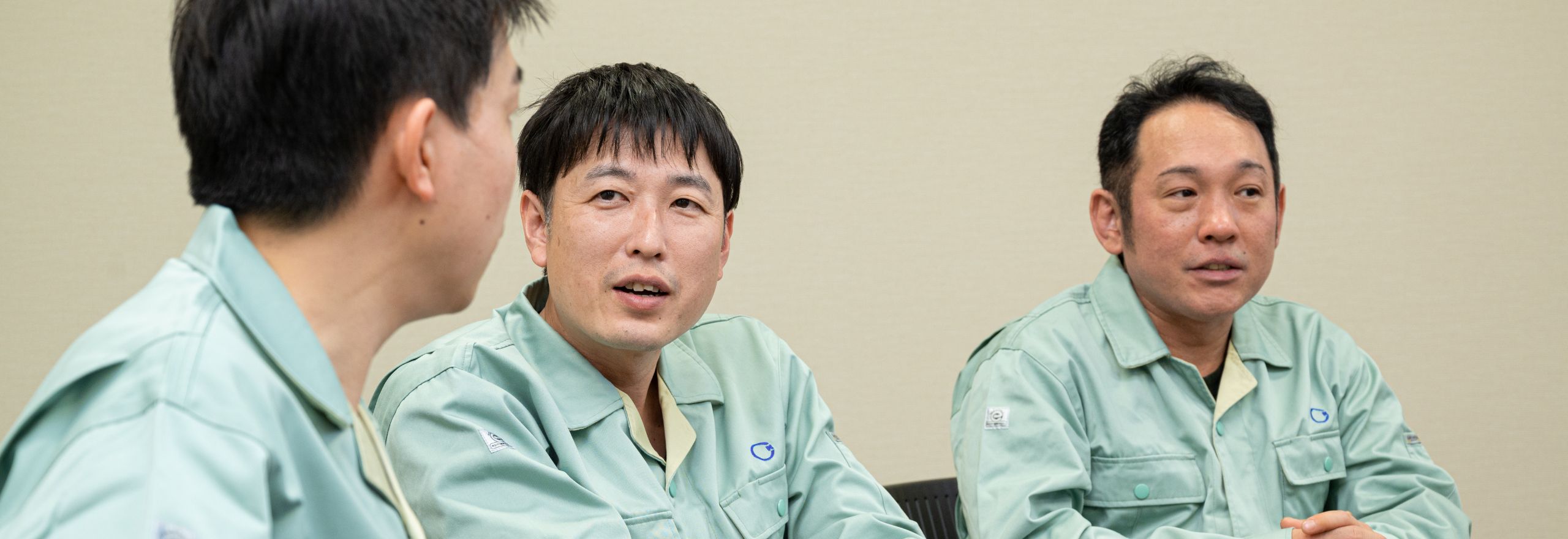
量産化にあたって苦労したことはありますか?
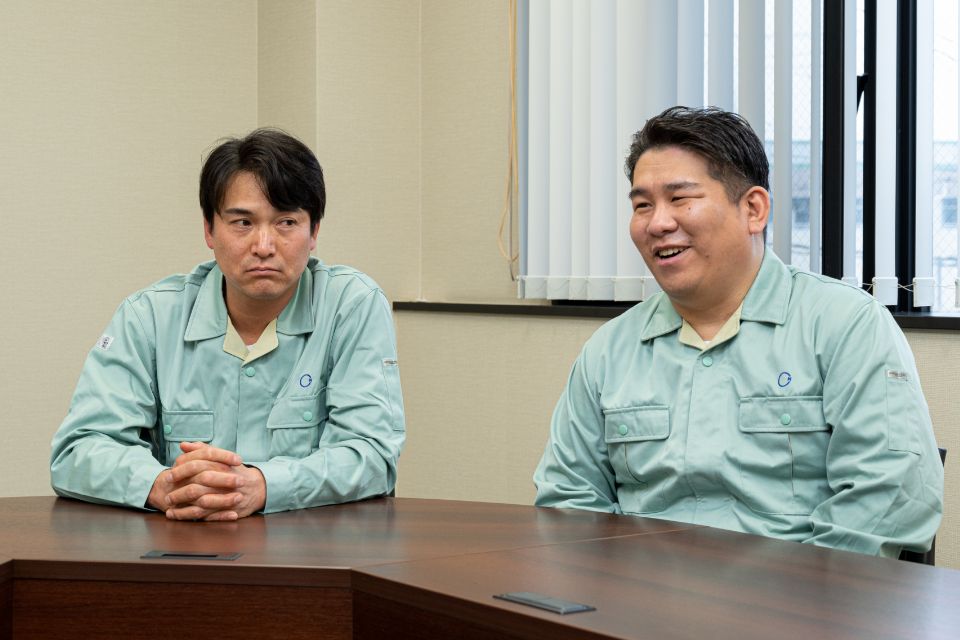
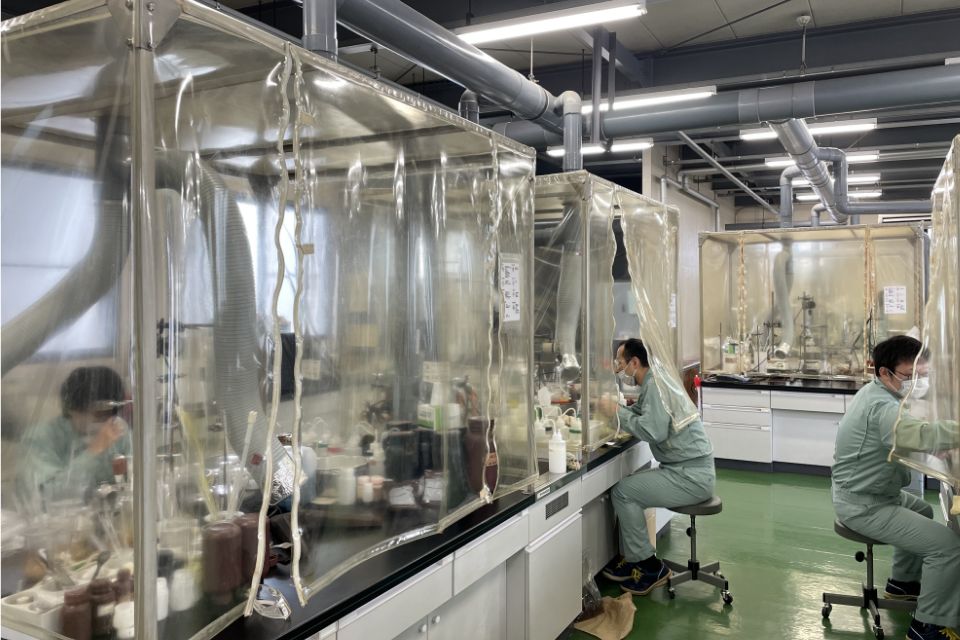
Nikkacureの開発で、どのような知見が得られましたか?
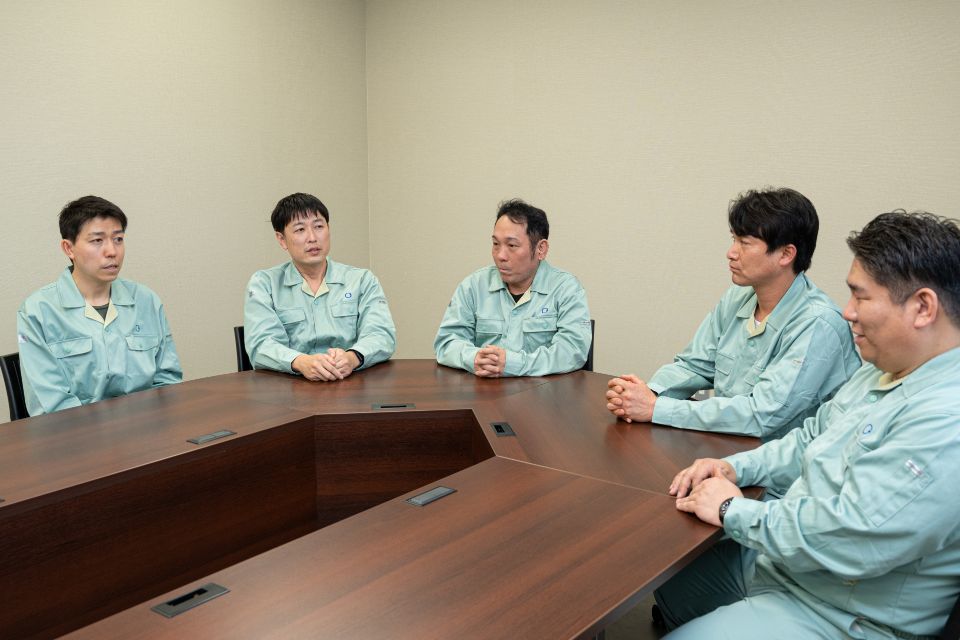
今後はどのような製品を開発していきたいですか?
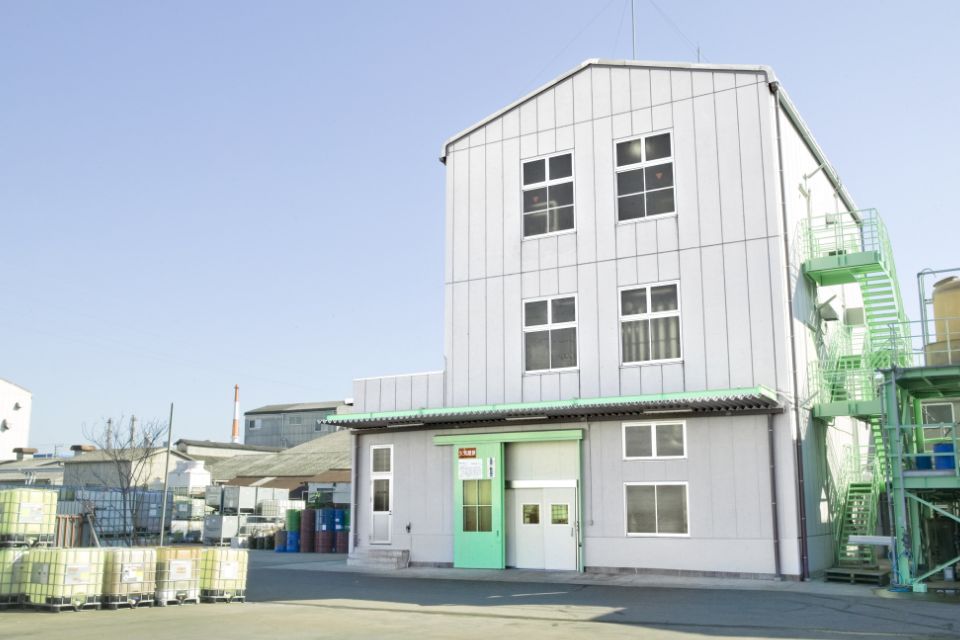